Choosing READY-FLEX® Flexible Shafts with Casing
Casing is usually necessary for shaft lengths that exceed 8 inches. Also, casing is recommended when the environment is dirty, dusty, or corrosive or when the shafts are run at high speeds in exposed areas where injury can occur. Refer to the chart below to find specifics on each assembly diameter.
​
Ready-Flex® Flexible Shafts with Casing are used for many types of applications. Their protective casing holds the grease in the assembly and keeps dirt and dust away from the rotating shaft. The casing also guards against potential injury from the rotating shaft coming into contact with an operator.
​
They come with either Ball Bearing or Oilite Bearing couplings. Ball Bearings are typically used for higher speeds and greater loads.
Oilite Bearings are used for slower speeds, control applications, and lighter loads. Both Oilite and Ball Bearings Assemblies are available in ten (10) different diameter sizes: .130, .150, .187, .250, .312, .375, .500, .625, .750, and 1.000.
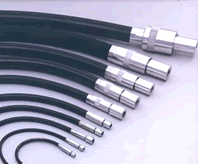
Bi-Directional or Uni-Directional?
Uni-Directional (Power-FLEX™)
These shafts are designed for continuous operation, maximum torque carrying ability, and torsional stiffness in only one direction of rotation: either clockwise or anti-clockwise when viewed from the driving end. The performance of a Uni-directional shaft will fall off dramatically if operated in the opposite direction.
Bi-Directional (Steady-FLEX™)
These shafts are designed to rotate in both clockwise and anti-clockwise directions. They have more balanced physical properties that allow them to operate in either direction of rotation.

Torque Requirements
This is the maximum continuous torque (in-lb or N-m) that you will be transmitting through the shaft.
This will determine the diameter of the shaft required for your application.
Start up torques-or short duration peak torques- may safely be 20% higher.
​
If you are measuring your load in Horsepower, you must convert to in-lb using the Torque-Horsepower conversion chart , or use the following formula:
​
HP x 63,000
Torque = ---------------
RPM
Minimum Bend Radius
There is a direct relationship between operating torque and operating radius; as the radius gets smaller the torque capacity of the shaft reduces.
​
In tighter bends the wires rub against each other more forcefully increasing the friction, heat, and stress.
The minimum radius can be calculated using the following formula:
​
​
x ² + y ²
R = ----------
4x

Minimum Bend Radius
Charts to Select the Correct Shaft
Depending on your application's direction of rotation (see diagram above) and measurement units, click on the appropriate chart to choose the correct Flexible Shaft for your application:
​
Uni-Directional (English Units) chart
Uni-Directional (Metric Units) chart
Bi-Directional (English Units) chart
Bi-Directional (Metric Units) chart
​
Locate the column with your minimum bend radius in the charts. Start at the top, go down the column until you find the corresponding shaft diameter that is rated for your least torque load. If you click the link below the chart, you can see more specifications for that shaft.
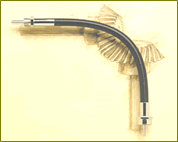
Bending or Torsional Stiffness
If two or more types of shafts of the same diameter meet your torque requirements, it is desirable to choose the shaft with the lowest bending stiffness, since it correlates to lower "torque to rotate" which is a measure of the internal friction in the shaft.
​
If torsional deflection i.e. the shaft twisting under load is a concern, then look at the corresponding torsional stiffness values for the shafts that meet your torque and minimum radius requirements . From these, choose the shaft that best fits your deflection needs.
Operating Speed
This is the maximum continuous speed in RPM's for a shaft under load.
Check the Specification Charts to see that your speed is within the design limits of the shaft.
As the speed increases the level of power transmitted can increase as the torque load is reduced proportionally to the increase in the shaft speed.
From this you can see that Flexible Shafts like to be run fast so as to reduce torque load.
*Excessive speed, especially in tight bend radii for extended periods, can cause heat buildup and premature failure.
Length
Determine the proper length (in inches) of the overall shaft assembly by closely approximating all bends and offsets.
​
Measure the length along the centerline of the shaft.

Casing
A Flexible Shaft casing is recommended when assembly lengths exceed 8 inches or speeds exceed 50 RPM.
Casings serve many purposes such as:
​
Protect the shaft from moisture, dust and dirt while retaining lubrication
Prevent injury to the operator by contact with an unprotected rotating shaft at high speed
Provide a continuous guide for the enclosed shaft for smooth operation
Prevent the shaft from helixing, or looping, during operation under torsional loads
Control the bending of the enclosed shaft by guiding it into more natural and gradual bends while limiting how tight a bend radius it can achieve
Ready-Flex® Flexible Shaft with Casing assemblies are available in both Oilite and premium low friction Ball Bearing couplings.
Click on the type that fits your requirements and determine which bore diameter you need (A, B, C, or D).